Contact: Danko Van Der Laan or Kristin Roberts
TALLAHASSEE, Fla. — Scientists and engineers working at the National High Magnetic Field Laboratory have successfully tested a new kind of magnet that could be used in next-generation particle accelerators and compact fusion machines. Their work was published last week in Superconductor Science and Technology.
The magnet coil, wound from a cable using a special superconductor called REBCO (rare earth barium copper oxide), features a novel design that can carry a very high current and hold up to the stresses created by high magnetic fields. Superconductors are materials that conduct electricity with no resistance, typically under specific conditions such as very low temperatures. This means the electricity requires no voltage to push it through the superconductor (unlike copper, for example), making the power essentially free.
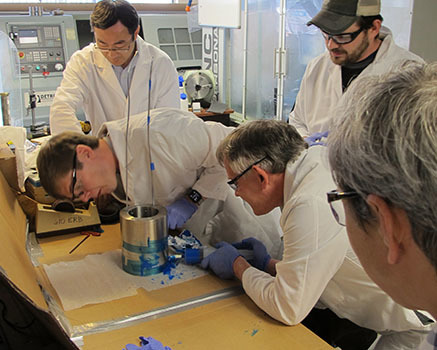
The MagLab's Ulf Trociewitz (third from left) injects epoxy into the magnet to fill the space between the windings and outer shell. Also pictured are (left to right) Xiaorong Wang of Lawrence Berkeley National Lab; Jeremy Weiss of Advanced Conductor Technologies; and Trociewitz, James Gillman and Dima Abraimov of the the National MagLab.
Photo credit: Danko van der Laan
Superconducting magnets have been around for decades: They are at the heart of every MRI machine. REBCO is a relatively new material and a type of high-temperature superconductor (HTS), a class that operates at higher temperatures (though still quite cold) than the conventional superconductors used in MRIs. HTS materials are among the hottest areas in physics research today.
The magnet was tested in November at the National MagLab's Applied Superconductivity Center in collaboration with Danko van der Laan, founder of Advanced Conductor Technologies (ACT) and the inventor of the cable from which the magnet was wound.
It is not the world's first REBCO magnet. In fact, the National MagLab is home to one of the world's strongest superconducting magnets, which was made in part with REBCO and generates a field of 32 teslas (tesla is a unit of magnetic field strength; a typical hospital MRI machine generates about 2 or 3 teslas).
The new magnet introduces a very different design. Magnets are built in the shape of coils; when electricity is run through, it generates a strong magnetic field in the center of the coil. The REBCO coils of the 32-tesla magnet were made by winding 9.4 kilometers (5.8 miles) of a tape-like form of REBCO into a coil. The ACT magnet was wound from what van der Laan calls a Conductor on Round Core (CORC®) cable containing 28 REBCO tapes arranged in 14 layers.
To test the coil, the research team placed it inside a larger, 14-tesla superconducting magnet (made with conventional superconductors). They turned both on, then ramped the test coil up to 2.7 teslas, marking the first successful test run for a magnet of its kind.
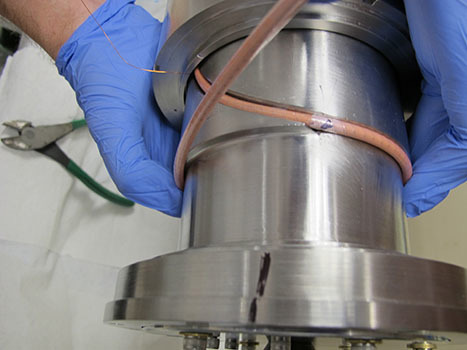
Completing the most difficult part of the magnet winding, when the CORC cable is guided into the first magnet layer.
Photo credit: Danko van der Laan
The purpose of putting the CORC® coil inside the stronger magnet was to make sure it could withstand the forces generated by a strong magnetic field. It passed with flying colors, withstanding the stresses while carrying a very high current of 4,400 amps.
Van der Laan said the test proves that CORC® technology, 10 years in the making, has matured enough to be used in actual high-field magnets.
"It really shows that we have a very good handle on the technology at this point," van der Laan said. "It is like a graduation. Now it's ready for a real magnet program where we build a real, large magnet that generates even more field than this coil had."
Van der Laan designed the CORC® cables to address some of the challenges of working with REBCO, which is quite hard to fabricate in tape form and even harder to fabricate perfectly. Flaws in the tape can bring a sudden hault to superconductivity, like a semi stopping suddenly on a packed freeway, causing the magnet to fail. But when layers of REBCO tape overlap, as in van der Laan's design, a flaw isn't such a big deal: The current just jumps to an adjacent tape, like a speeding car bypassing the semi using an extra lane. This makes the design inherently safe, stable and forgiving, he said.
"If the tapes are not perfect," van der Laan said, "you don't really care."
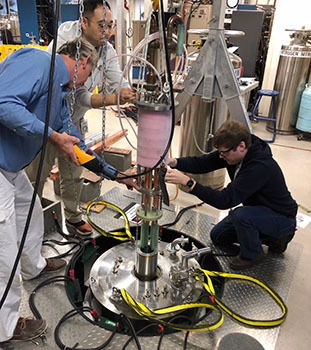
The team inserts the CORC magnet into the bore of a larger, 14-tesla magnet for testing. From left to right: Van Griffin and Youngjae Kim from the National MagLab with Jeremy Weiss of Advanced Conductor Technologies.
Photo credit: Danko van der Laan
The robust design will make it easier to ramp the magnet’s field quickly up and down, van der Laan added, another requirement for magnets used in particle accelerators and fusion machines. The technology may also be useful at the MagLab itself one day, which is always developing stronger magnets that scientists use to examine materials, biological tissue and other samples to make new discoveries. REBCO is one of several materials and technologies under consideration for next-generation magnets.
Van de Laan said the MagLab's expertise and facilities were critical to the test’s success. "There's no other place in the U.S. that I'm aware of that could have done this," he said.
"The special setup with the new 14-tesla magnet offers an excellent facility for more HTS cable and magnet research and development," said MagLab scientist Ulf Trociewitz, who developed the test bed for ACT's magnet. "It all worked very well, and we're looking forward to testing more prototype coils."
In addition to van der Laan and Trociewitz, other scientists working on the project include: Jeremy Weiss of ACT; Dima Abraimov, Lance Cooley, Daniel Davis, Ashleigh Francis, James Gillman, Van Griffin, Youngjae Kim, David Larbalestier, George Miller and Huub Weijers of the National MagLab; and Xiaorong Wang of Lawrence Berkeley National Laboratory.
This research was done as part of a Small Business Innovative Research grant from the U.S. Department of Energy, Office of High Energy Physics, which encourages small businesses to partner with academia to develop new technology. The National MagLab is funded by the National Science Foundation (DMR-1644779) and the State of Florida.
Story by Kristen Coyne