"Machine shop."
Let your mind construct a mental image of those words, and within seconds you’ve probably got a scene involving dirty overalls, metal shavings flying pell-mell through the air, a blaring radio and fingernails encrusted in grease. Throw in a half-eaten box of day-old donuts set atop a lathe somewhere.
Now erase that image. It has little in common with the MagLab’s machine shop — except for the classic rock. OK, and the occasional box of Krispy Kremes brought by a happy customer.
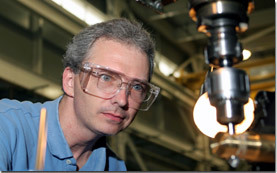
Engineer Andy Rubes machines an instrumentation rotator for a magnet probe.
This 4,000 square feet of orderly, tidy space is the Ritz of machine shops. In fact, one might almost be tempted to call it a machine boutique.
Although the six seasoned machinists who work there would likely blanch at the characterization, it is in some ways fitting: These guys don’t manufacture run-of-the-mill auto parts: they do extremely high-end, custom work, often using expensive or exotic materials such as gold or beryllium copper. They collaborate with some of the most accomplished scientists in the world. They use sophisticated design and engineering software, and operate a wide range of machinery from the conventional drill press to the state-of-the-art, computer-controlled lathe. Their craftsmanship requires the exactness of a watchmaker, the patience of a parent, and the depth of experience that only a staff with a combined 170 years in the field can offer.
The staff works on hundreds of projects a year. Many of them are repairs or modifications to existing equipment. Most involve the creation of prototypes — unique parts made for the first time.
Scott Hannahs, Chief of User Research Instrumentation with the lab’s DC Field Facility, says the lab’s unique magnet instruments, capable of measurements done nowhere else in the world, are made possible by the machine shop’s tools and talents.
“These are machinists who can design and build the bizarre parts that we imagine,” said Hannahs. “They can work with us as collaborators and help us refine our ideas into actual, real, physical instruments to make our measurements.”
In the machine shop you’ll find a very neat mix of ingenuity and skill, high-end problem solving and good-natured wise-cracking. Put on a pair of safety glasses and come see for yourself.
High-end tools and experienced hands
Scientists and engineers who use our magnets, whether from the in-house staff or visiting from another institution, often need a special piece of equipment for their experiments. It might be a probe — a long, tube-like device containing the researcher’s sample that is inserted into the bore of a magnet. Or it might be a pressure cell; scientists sometimes put their sample in one of these small containers in order to observe how it responds to the combination of high fields and high pressure. Or it might be a specialized rotator, a small cage affixed to the probe that allows the sample inside it to turn during the experiment.
Just about everything made in the machine shop starts with a concept. A scientist might draw the device or part she needs by hand or with a computer, but her design abilities typically end there.
That’s where Vaughan Williams, the machine shop’s group leader and coordinator of Research Programs and Services at the lab, steps into the picture.
“We understand what it takes to make parts in a prototype setting,” he said.
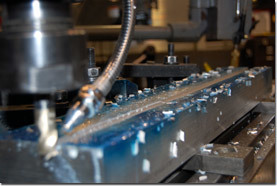
A milling machine is used to dig a groove into a bar of aluminum.
Collaborating closely with the scientists, Williams takes the drawing to the next phase, creating a virtual model of the needed part with special design software. That model is then uploaded into a computer-aided manufacturing (CAM) program that spells out which tools are best suited to fashion the part’s various features. Thanks to the software, the staff can test out machining operations virtually, catching errors while they’re still cheap and easy to fix.
A machinist may then fashion the object manually, using the shop’s traditional milling machines, drill presses, lathes and grinders. But for projects requiring multiple copies of the part, or for especially complex designs, machinists will opt for one of several Computer Numerical Control (CNC) machines, which will execute orders it receives from computer code generated by the CAM software. For the most complex projects, machinists may have to fashion specialized drills or boring bars before beginning the actual part that those tools will create.
In addition to exercising their craft, the machinists teach it. Everyone benefits when scientists know more about the design and manufacturing process. That’s why machinist John Farrell holds several classes a year for students and post-docs at the lab, instructing them on what to keep in mind when dreaming up tools for their research (for example: avoid small, square holes).
Collaboration is key
To illustrate how scientists and machinists work together at the lab, let’s follow the creation of one particular part designed and built in 2008.
Ju-Hyun Park, a postdoctoral associate who studies how superconductors behave at extremely low temperatures, needed a special rotator for an experiment involving CeCoIn5, a superconducting material made up of cerium, cobalt and indium. Most rotators, as they turn, sometimes brush up against wires inside the probe — of no consequence for most experiments, but something that could interfere with the results of the experiment Park had designed. Depending on the angle at which his sample was positioned, Park hoped to observe different properties in CeCoIn5 as he examined the superconducting vortex structure of the material.
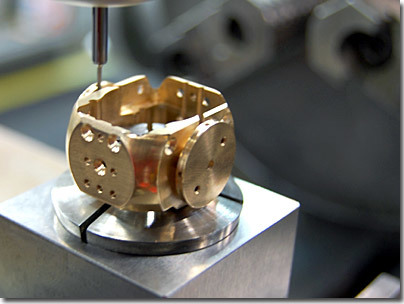
Park's nearly completed rotator on the milling machine.
“For this particular experiment, I needed something smooth that doesn’t hit anything,” he said.
Park, who has some design experience, produced his own virtual model of the rotator he envisioned. But his skills could only take him so far. “I draw things unreal sometimes,” he said. “In my head, it’s OK.”
But in actual science, it’s not OK, which is why Park relied on the expertise in engineering, materials and design found in the machine shop.
“They know more features than we do,” said Park, who has worked on several projects with the machine shop team, including a specialized probe. “They can suggest, ‘What if you do this? What if you do that?’ I don’t really have knowledge of engineering.”
The machine shop is just across the hall from the Millikelvin Facility where Park works, so he and the machinists can confer easily and quickly when questions arise. As a result, not only are parts produced much more quickly than if they were ordered outside the lab, they are also of higher quality — just what the scientist ordered. And because good communication means fewer mix-ups, costly misunderstandings are avoided.
“Throughout, interaction is key,” Park said. “That’s the only way you can get a good part.”
Park collaborated closely with machinist Danny McIntosh on the rotator project. Because of its complex design, both CNC and manually operated machines were used to turn and shape blocks of beryllium copper into a unique science tool fit for an art museum. The shop’s most high-tech apparatus, a six-axis wire electrical discharge machine (EDM), was used to nail the tricky geometry of the center of the ¾ inch-wide part. Then McIntosh manned the milling machine to craft the holes and grooves that completed the project. Some 30 hours later, Park had a one-of-a-kind rotator for his experiment.
“It’s the first time we ever made a rotator like that,” said McIntosh, who, like his shop mates, will relent with a serious answer only after two or three jocular ones. Continuing in a serious tone, the 33-year machining veteran added that the challenge of creating something for the first time, combined with the chance to work with some of the best tools and scientists around, make his a pretty awesome job.
That, he quipped, plus the donuts.
Bringing ideas to life
The below image gallery illustrates, from concept to end product, how machinists turn scientists’ ideas into reality. The images portray how Danny McIntosh (milling machine) and Vaughan Williams (EDM) created a continuous rotator, made of beryllium copper, for a magnet probe based on scientist Ju-Hyun Park’s design. It took 30 hours to complete the rotator which was used to study the behavior of CeCoIn5 (a superconducting material made up of cerium, cobalt and indium) at extremely low temperatures. View computer-aided design of the rotator.