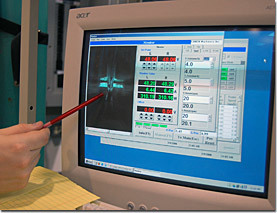
Monitoring a crystal growth.
A lot of scientists who do research at the MagLab are condensed matter physicists; they study solid matter. Most matter is polycrystalline, meaning it's made up of lots of tiny crystals that are all jumbled up, facing in different directions.
If you want to understand matter, it's more helpful to look at one large single crystal, rather than a piece of matter made up of a bunch of them. In that single crystal, all the constituent molecules, atoms or ions are aligned in the same direction. So when physicists put them in magnets and take various measurements, they will get better data. In general, the bigger the crystal is, and the higher its quality, the more useful it is to the scientist. That's why at the MagLab we grow a lot of our own crystals using a tool called an image furnace.
Two ways to grow crystals
There are two ways to grow crystals: a traditional way and a modern way.
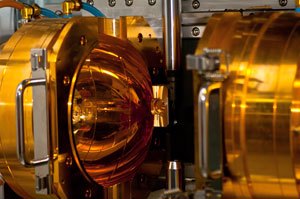
A lamp in the image furnace.
The traditional way to make crystals is to mix your ingredients together, put them in a container, and heat the mixture to a very high temperature. That heat causes the atoms to jostle around and react with one another. As the mixture slowly cools, crystals form, all (hopefully) lining up in the same direction. The heat is a little like shaking up a tin of pecans or box of Legos: The pieces will tend to settle in the same orientation, lining up next to one another, because that's the most efficient use of space. This method is called flux growth because a flux, or liquid solvent, is sometimes added to the mixture to help the crystal form.
The more modern way to grow crystals for most applications is with an image furnace. One of the main advantages of this approach is that it doesn't involve a container, which can contaminate the crystal with impurities. Another bonus is that you can actually watch the crystal as it forms. This helps the crystal grower to better monitor and control the delicate process, which can last several days. The term "image furnace" comes from the fact that the mirrors make an image of the light source on the rod heating it up.
Precision cooking
Crystal growers using an image furnace prepare ingredients in pretty much the same way as in flux growth, although generally no flux is used. The polycrystalline material is then formed into two small rods, a few centimeters long and a few millimeters wide. Inside the furnace, one rod is suspended from a tiny platinum wire and the other is positioned exactly below it, with about a millimeter of space in between. That very small area, where the two rods barely meet, is the hot zone. Two lamps on either side of this set-up generate the heat, and mirrors positioned behind the lamps reflect and focus that heat at the precise spot where the two rods almost meet. Because the heat is pinpointed in this way, most of the furnace remains relatively cool, while the hot zone itself reaches temperatures as high as 2400 degrees Celsius. By varying the voltage and amperage of the lamps, the furnace operator can precisely control the heat in that zone.
Diagram of an image furnace.
As the hot zone heats up, the bottom tip of the upper rod begins to melt and drip onto the rod below it, the droplet held in place by surface tension. The molten material cools down as it drips down onto the bottom rod, right below the hot zone. As it cools, the jumbled-up atoms align, and a single crystal begins to form atop the bottom polycrystalline rod. The top rod is lowered very slowly – as slowly as half a millimeter per hour – and revolves, on average, about 20 times a minute. In this way, the molten area is maintained between the two rods. Bit by bit the liquid drips onto the bottom rod, and bit by bit the crystal forms, each atom or molecule (hopefully) aligning with the ones that formed right before it.
Photos (taken by the built-in camera) of a growing crystal (Nd3Ga5TiO14).
Crystal growing is as much an art as it is a science. Every crystal is different, requiring different recipes, cooking time, temperature and rod control rates. Because the heat is so focused, a camera can be mounted inside the furnace, allowing the operator to keep track of the forming crystal on her computer screen.
Studying a material in large, single crystal form is the first step in understanding it. Recently scientists have been studying single crystals of high-temperature superconductors and colossal magnetoresistance materials. By putting these crystals in magnets and measuring properties such as heat capacity and resistivity, they hope to uncover some of the mysteries of how they work.
Thanks to Chris Wiebe, associate professor of physics at the University of Winnipeg/University of Manitoba and a member of the MagLab's User Committee, for serving as the scientific advisor on this page.
By Kristen Coyne